Plastic Injection Molding - The Facts
Wiki Article
Getting The Plastic Injection Molding To Work
Table of ContentsThe Best Strategy To Use For Plastic Injection MoldingThe Greatest Guide To Plastic Injection MoldingHow Plastic Injection Molding can Save You Time, Stress, and Money.Our Plastic Injection Molding Diaries
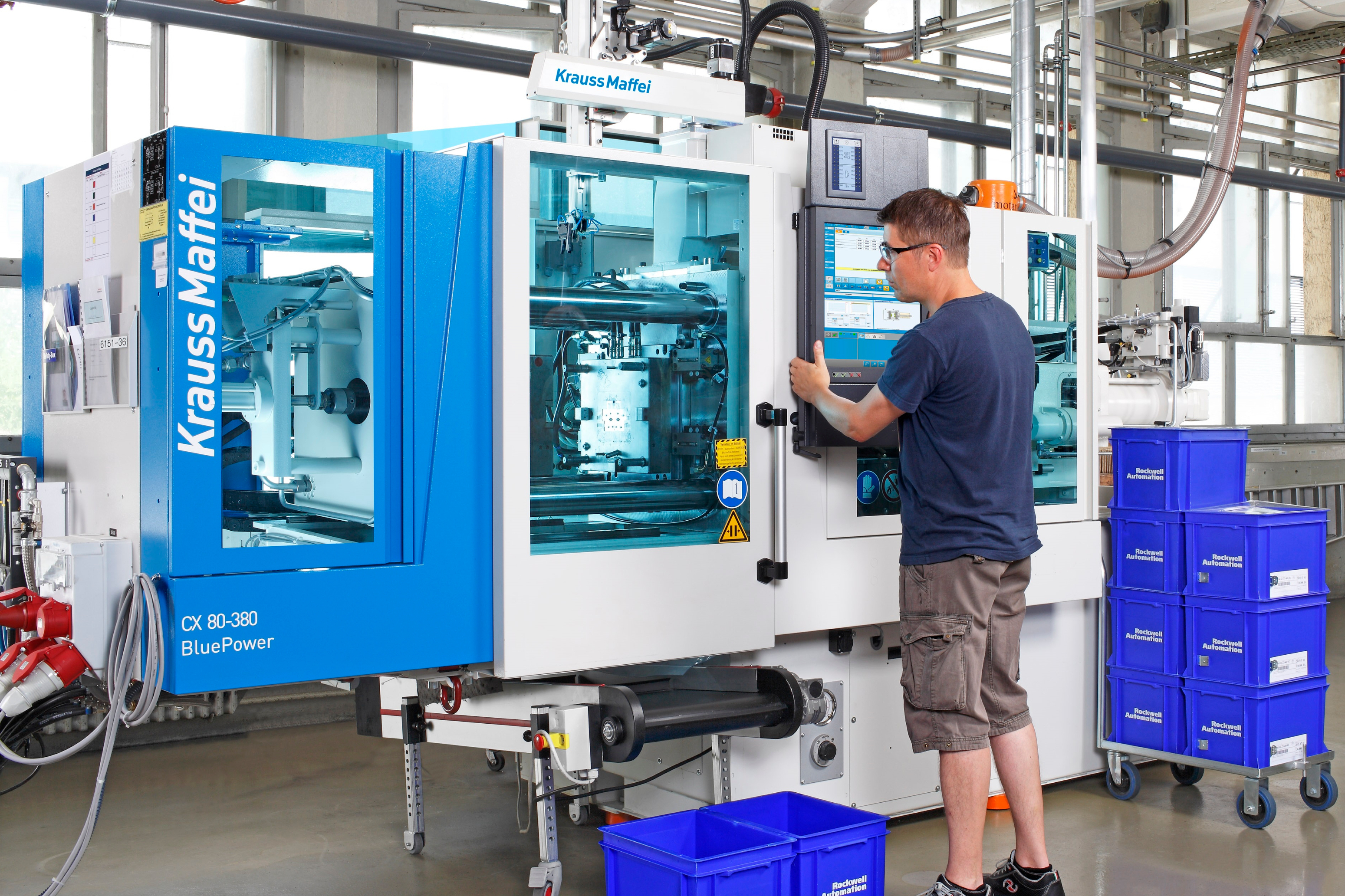
If you intend to explore further, the guide covers sorts of mould devices, in addition to special ending up procedures such as colours & plating. Words that are underlined can be found in the reference in the appendix ... Part I: Moulding: The Essentials The Advantages of Shot Moulding Plastic shot moulding is an extremely specific procedure that provides numerous advantages over other plastic processing approaches.
Precision is best for really intricate parts. You can hold this moulding in the hand of your hand as well as it has bosses, ribs, metal inserts, side cores as well as openings, made with a sliding shut off function in the mould device.
The liquified plastic cools & hardens into the form inside the mould device, which after that open up to allow the mouldings to be ejected or gotten rid of for evaluation, distribution or second procedures. Phase 1Material granules from the hopper feed into the heated barrel & revolving screw. Material melted by warmth, rubbing & shear pressure is forced with a check shutoff to the front by the revolving screw ... Component III - Past the Basics - Tooling Options Manufacturing in China can save you a lot of expense, however it can include issues such as shipment hold-ups, miscommunications, inferior high quality as well as the documents surrounding importation. Utilizing a UK moulder with existing ties to China can eliminate the risk and still result in cost-saving ... Cavity - The part of a shot mould device that provides the plastic product its shape, that does the actual moulding of the plastic. See mould tool phase on web pages 5 and 6 for all terms linked with the mould tool Cycle time - The time it takes for a mould cycle to be finished, i (plastic injection molding).
from material feed & melting; material injection; cooling time cooling down ejection to the re-closing of the mould tool ready device the next cycleFollowing Draft angles - The wall surfaces of a moulded part need to be somewhat tapered in the direction in which the component is expelled from the mould tool, to permit the part to be expelled easily.
Ejector stroke - The pushing out of ejector pins to eject the moulded component from the mould device. Ejector stroke speed, length as well as timing requires to be thoroughly regulated to stop damage to the ejectors as well as mould device, yet at the same time make the moulding cycle as short as feasible.
The Best Guide To Plastic Injection Molding
Overlocking - When a mould tool has actually been established right into a moulding equipment incorrectly, triggering the device to close also tough therefore damaging the mould device Component repeatability - The capacity to develop the same plastic part-times after time Span - Completely straight corners are impossible to eject from the mould tool.Ribs - When a plastic part has slim wall surfaces, ribs are included to the style to make the thin walls stronger Side cores - Side activity which generates a feature on a moulded component, at an opposing angle to the typical opening direction of the mould tool. The side core needs to be able to my review here withdraw as the plastic component can not be expelled otherwise.
Walls - The sides of a moulded part The message on this page is a sample from our complete White Paper 'Shot Moulding for Buyers'.
Injection moulding is commonly used for making a variety of components, from the smallest parts to entire body panels of vehicles. Advances in 3D printing innovation, using photopolymers that do not thaw throughout the injection moulding of some lower-temperature thermoplastics, can be made use of for some easy shot moulds. Injection moulding uses a special-purpose device that has 3 components: the shot device, directory the mould and the clamp.
What Does Plastic Injection Molding Mean?
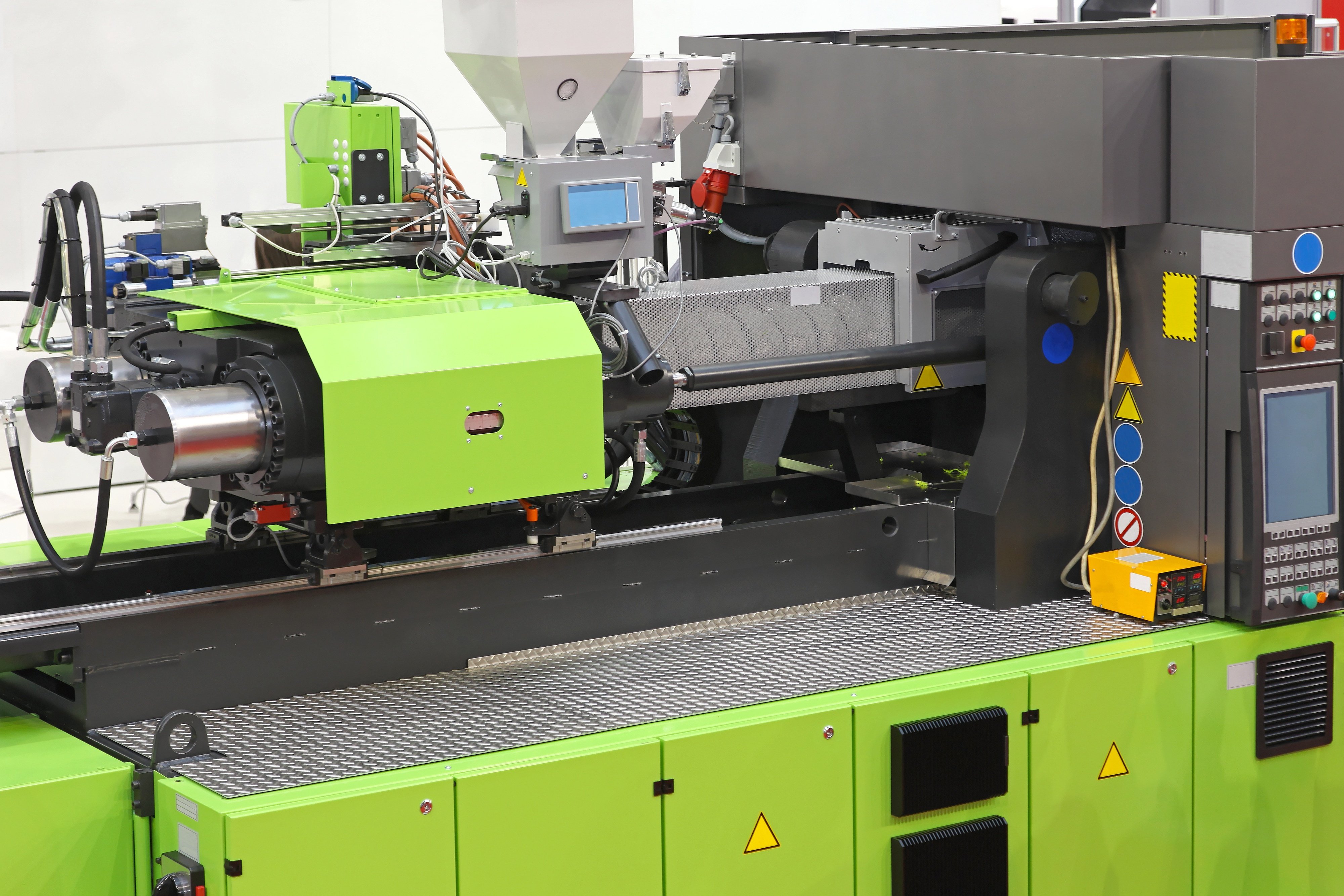
In several cavity moulds, each cavity can be the same as well as develop the same components or can be special as well as form numerous different geometries during a solitary cycle. Moulds are typically made from tool steels, yet stainless-steels and aluminium moulds are ideal for specific applications. Aluminium moulds are normally ill-suited for high quantity production or get rid of slim dimensional tolerances, as they have substandard mechanical residential or commercial properties and also are more prone to use, damages, as well as deformation throughout the injection as well as securing cycles; nevertheless, aluminium moulds are cost-effective Recommended Reading in low-volume applications, as mould manufacture expenses and also time are significantly lowered.
When sufficient material has collected, the product is required at high pressure as well as speed right into the part forming cavity. The exact quantity of contraction is a function of the resin being used, and also can be reasonably foreseeable. To stop spikes in pressure, the procedure typically uses a transfer position representing a 9598% complete tooth cavity where the screw shifts from a consistent rate to a continuous stress control.
When the screw reaches the transfer position the packaging pressure is applied, which completes mould dental filling and makes up for thermal shrinking, which is rather high for thermoplastics about numerous other materials. The packing pressure is used until eviction (cavity entryway) solidifies. Due to its little size, eviction is typically the starting point to strengthen with its entire thickness.: 16 Once eviction strengthens, say goodbye to material can get in the dental caries; appropriately, the screw reciprocates as well as acquires product for the next cycle while the product within the mould cools down so that it can be expelled as well as be dimensionally stable.
Report this wiki page